Construction Management using Digital Twin
Construction Management using Digital Twin is a recent technology gaining popularity nowadays. The construction industry has long been characterized by complexity, delays, and cost overruns. However, recent advancements in technology, particularly the development of digital twins, are transforming how we manage the construction projects. By creating virtual replicas of physical assets, digital twins enable real-time monitoring, predictive insights, and better decision-making throughout the lifecycle of a construction project.
What is a Digital Twin?
A digital twin is a dynamic, real-time digital representation of a physical object, process, or system. In construction, a digital twin can be thought of as a virtual model of a building, infrastructure, or construction site that is continuously updated with data from sensors, IoT devices, and other real-world inputs. This allows construction managers and stakeholders to monitor and analyze the physical asset remotely, simulate potential outcomes, and optimize the project’s execution and operation.
Unlike static 3D models, digital twins are live, data-driven representations. it means, they are constantly updated with real-time information about the state of the physical asset. These models can simulate various scenarios, identify potential issues, and help optimize performance.
Example of Digital Twin
Let’s consider a real-world example of digital twin technology in construction. Below is an example of our digital twin platform to monitor a road intersection project in New South Wales.
Basically, we use a mobile laser scanner, high-resolution 360 panoramic camera, and UAV-based laser scanner to capture the data. By having a digital update of the construction project, we can check current condition and detect changes between each scanning. We can see each data from 360 view to get the most detailed information for each section.
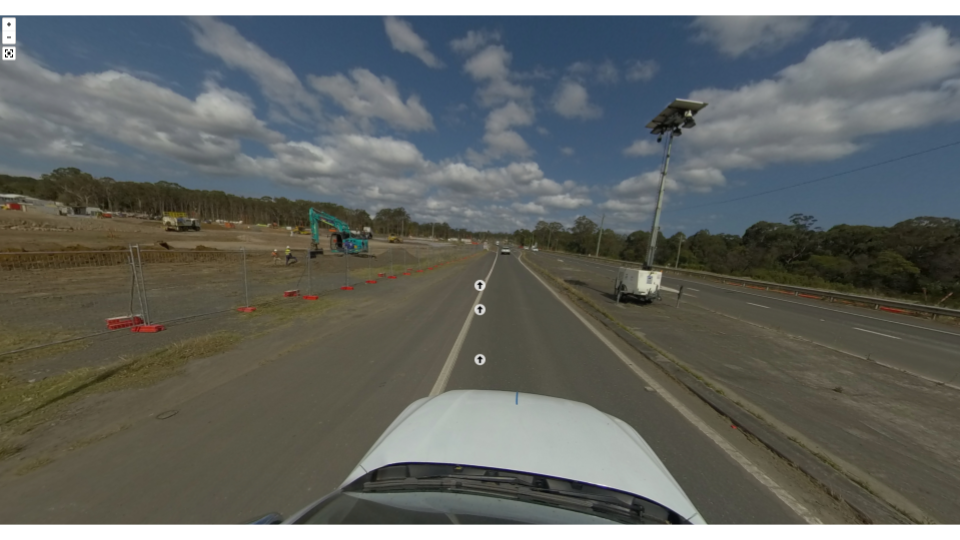
Change Detection
Change detection between different scans in an infrastructure project involves comparing images, point clouds or other 3D data sets captured at various stages of construction or maintenance to identify alterations or deviations. This process is crucial for monitoring progress, ensuring that construction adheres to design specifications, and detecting potential issues such as structural deformations, material degradation, or unauthorized modifications. By analyzing differences between scans taken over time, construction managers can quickly pinpoint areas of concern, enabling proactive decision-making, reducing rework, and ensuring the project’s safety, quality, and compliance with regulatory standards.
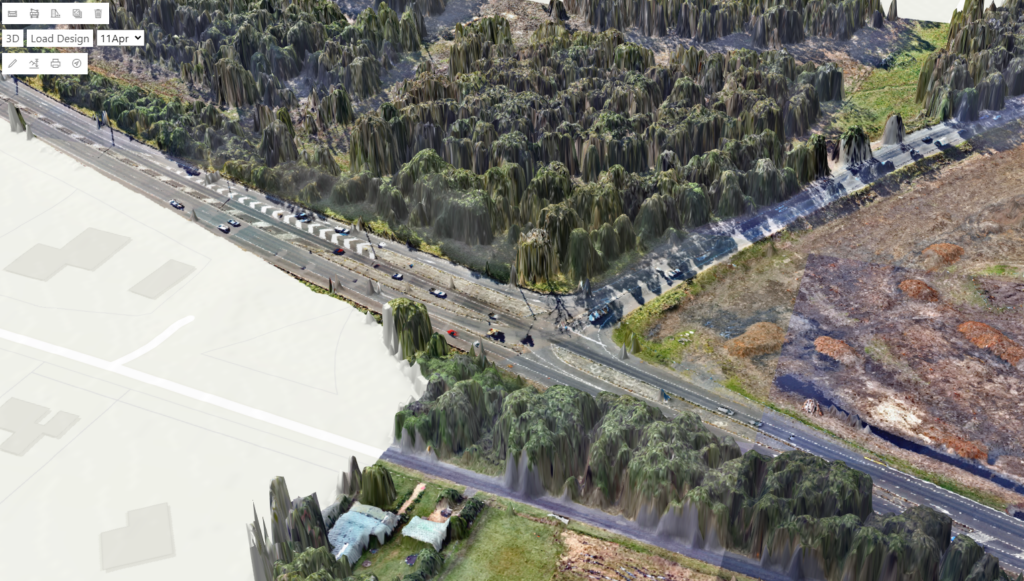
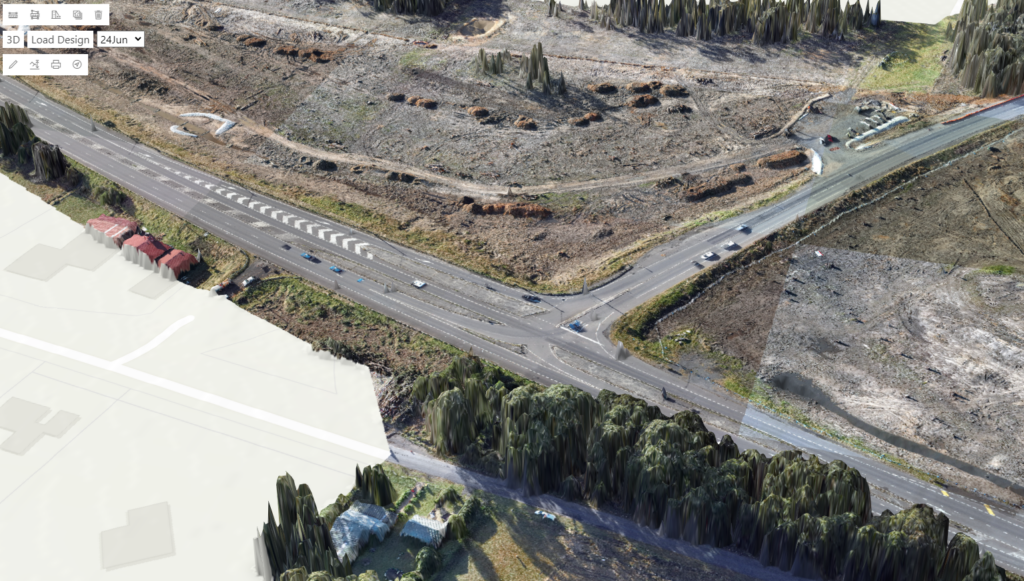
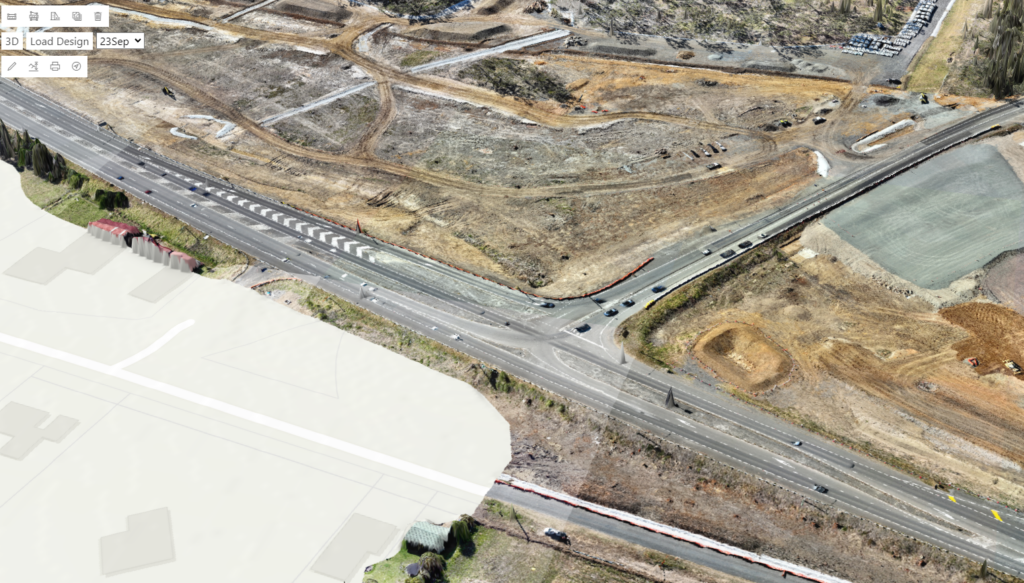
Benefits of Using Digital Twin in Construction Management
Implementing digital twins in construction management offers several benefits that can greatly improve project outcomes.
Improved Project Planning and Design:
- Better Visualization: Digital twins offer a highly detailed, real-time representation of the project. It enables all stakeholders to see how the construction will look and function. This allows for more informed decisions during the design phase.
- Clash Detection: Digital twins can help identify potential conflicts between various systems (structural, mechanical, electrical) before they become costly issues in the field. This reduces the risk of design errors and rework.
Enhanced Construction Monitoring:
- Real-Time Tracking: Digital twins allow construction managers to track progress in real time. Sensors and IoT devices embedded in the physical structure feed live data into the digital twin. It provides insights into every stage of construction. The visualization of current construction condition also beneficial for progress monitoring.
- Performance Simulations: Construction teams can use digital twins to simulate the performance of the building or infrastructure under different conditions (e.g., weather changes, structural loads). This helps ensure the construction meets performance and safety standards.
Better Collaboration:
- Shared Data: Digital twins create a central repository of data. All the stakeholders, including architects, engineers, contractors, and owners can access the same data. This ensures that everyone is working from the same, up-to-date information, reducing misunderstandings and miscommunication.
- Remote Decision-Making: With digital twins, project managers and stakeholders can make informed decisions without being physically present on-site. This is particularly valuable in large or geographically dispersed projects.
Post-Construction Benefits:
- Building Lifecycle Management: After construction is complete, we can continue to use the digital twin for facility management. Owners can monitor the building’s performance, optimize energy usage, and plan maintenance activities based on real-time data.
- Asset Management: Digital twins help facility managers understand the building’s lifecycle, track the condition of assets, and ensure that maintenance schedules are followed to extend the lifespan of infrastructure.
Challenges of Using Digital Twin in Construction Management
Despite its many benefits, implementing digital twins in construction is not without challenges. Some of the key obstacles include:
High Initial Costs:
- Creating and maintaining a digital twin requires significant investment in hardware, software, and data management systems. For smaller construction firms or projects with tight budgets, the initial costs of implementing a digital twin might be prohibitive.
Data Integration and Management:
- Digital twins rely on large amounts of data from multiple sources, including IoT devices, sensors, and project management software. Integrating all this data into a single, cohesive model can be complex. Especially if the data comes in different formats or from incompatible systems.
- Data security is another concern as construction projects involve sensitive information that could be targeted by cyberattacks.
Training and Expertise:
- Implementing a digital twin requires a skilled workforce capable of working with advanced technologies. Some technology usually used are BIM (Building Information Modeling), IoT, and data analytics. Many construction companies may need to invest in training their staff or hiring specialized personnel to manage the digital twin.
Complexity in Real-Time Data Processing:
- The ability to update a digital twin with real-time data is a significant advantage, but it also adds complexity. Construction sites generate vast amounts of data, and ensuring that all the data is captured, processed, and displayed accurately can be a challenge. Poor-quality data could lead to inaccurate insights or poor decision-making.
Interoperability Issues:
- Many construction projects involve multiple teams using different tools and software systems. Ensuring that the digital twin can communicate and integrate seamlessly with all these systems can be challenging, especially if different stakeholders are using proprietary software that isn’t compatible.
Conclusion
Digital twin technology is rapidly gaining traction in construction management due to its ability to enhance project planning, increase efficiency, reduce costs, and improve collaboration. By providing real-time insights into the construction process, digital twins allow construction managers to make more informed decisions, optimize resources, and mitigate risks before they escalate.
However, despite the clear benefits, we need to address challenges like high initial costs, data management complexities, and the need for specialized expertise. As the construction industry continues to embrace digital transformation, digital twins are likely to become a standard tool for managing complex projects and improving the entire lifecycle of built assets.
In a world where precision, efficiency, and sustainability are becoming essential, digital twins offer a powerful solution to keep construction projects on track and ensure long-term success.
Category List
- 3D Point Cloud
- Artificial Intelligence
- Asset Management
- Digital Twin
- Featured
- Hardware
- Knowledge Graph
- LiDAR
- News
- Site Monitoring
- Vegetation Monitoring
- Virtual Reality
Recent Post
- Photogrammetry vs Image Processing: What’s the Difference and How Are They Used?
- Soil Adjusted Vegetation Index (SAVI): Definition and Application
- NDWI (Normalized Difference Water Index): Identifying Water Bodies with Remote Sensing
- Construction Management in the Digital Era: How GeoAI Transforms Projects with Data Analytics and AI
- What is Near Infrared (NIR)?