Digital Twin for Asset Management
Digital twin for asset management is beneficial to track our asset condition, arrange preventive action, and reduce the downtime of the asset. Digital twin is a replica of the physical asset that is connected and updated in a timely manner. We can have the digital twin of our asset to see the changes, deterioration, and performance. As a result, we can make a better management and maintenance for our infrastructure or asset.
The industrial landscape is filled with a wide range of assets, from towering wind turbines to intricate production lines. But as these assets age, keeping them running smoothly becomes a challenge. Enter the innovative concept of digital twins, virtual replicas of physical assets that hold immense potential for asset management.
What is a Digital Twin?
Imagine a perfect digital copy of your physical asset – a cooling tower, a factory floor, or even an entire airplane. This digital twin isn’t just a static image; it’s a living model that incorporates real-time data from sensors attached to the physical asset. This data includes temperature readings, vibration levels, and even structural health. By analyzing this data, the digital twin can predict potential problems before they occur, optimize maintenance schedules, and even simulate different scenarios to improve performance.
Benefits of a Digital Twin for Asset Management:
- Predictive Maintenance: Digital twins move us beyond reactive maintenance (fixing things when they break) to a proactive approach. By analyzing sensor data and historical trends, the digital twin can predict equipment failures before they happen, allowing for timely maintenance and preventing costly downtime.
- Reduced Costs: Predictive maintenance translates to significant cost savings. By identifying and addressing potential issues early on, you avoid expensive repairs and replacements down the line. Additionally, optimizing maintenance schedules minimizes unnecessary inspections and maximizes resource allocation.
- Improved Decision-Making: The data insights gleaned from the digital twin empower better decision-making. You can visualize the impact of different maintenance strategies, compare potential upgrade scenarios, and ultimately, extend the lifespan of your assets.
Case Study: Cooling Tower Digital Twin for Inspection
Let’s look at a specific example: a 120 meter height cooling tower built in the early 1980s, now showing signs of age-related wear and tear after 35 years of service. The primary goal? Understand the extent of deterioration, develop a comprehensive maintenance plan, and ensure the cooling tower continues operating for another 20 years.
Challenges of Traditional Inspection:
Conventionally, inspecting such a large and high structure can be difficult and dangerous. Scaffolding needs to be erected, and visual inspections are subjective, leaving room for error. Additionally, presenting the inspection findings in a way that clearly communicates the condition of the entire structure can be difficult due to tower’s size and height.
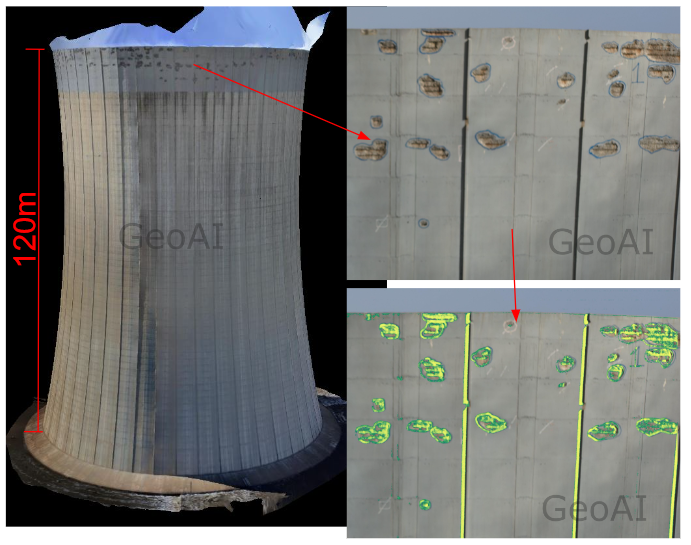
The Digital Twin for Asset Management Solution:
A digital twin of the cooling tower was created using 3D modeling. GeoAI utilized ground based and drone sensors to capture the cooling tower data. This digital replica provided a detailed, virtual representation of the structure, allowing engineers to remotely examine the tower. By using image analysis algorithm, GeoAI can automatically detect concrete defect on the captured images.
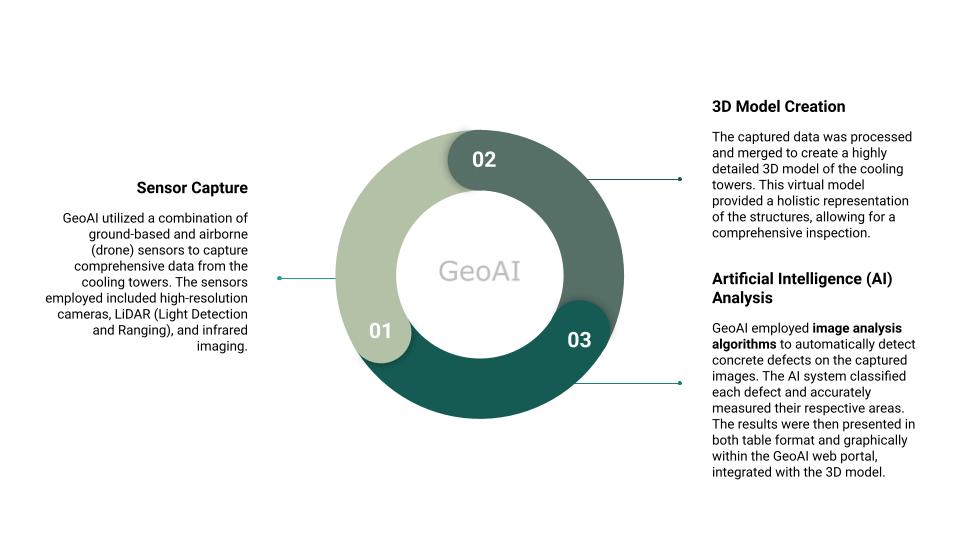
Benefits of the Cooling Tower Digital Twin:
- Detailed Inspection: The digital twin facilitated a thorough examination of the cooling tower, identifying areas of concrete spalling (flaking) and potential weaknesses.
- Improved Data Visualization: The digital model allowed engineers to visualize the inspection results in a clear and comprehensive way, pinpointing areas requiring immediate attention and those that could be monitored over time.
- Predictive Maintenance Plan: Based on the digital twin’s insights, a data-driven maintenance plan was developed, prioritizing repairs of the concrete and scheduling future inspections to maximize the tower’s lifespan.
This case study showcases the power of digital twins in asset management. By creating a virtual replica and leveraging sensor data, companies can gain valuable insights into the health of their assets. It ultimately extending their operational life and optimizing overall performance.
The Future of Digital Twins
Digital twin technology is still evolving, but its potential is undeniable. As sensor technology advances and data analysis capabilities improve, digital twins will become even more sophisticated, offering a truly holistic view of asset health and performance. This will empower businesses to manage their assets more effectively. As a result, it can ensures smooth operations and maximizing return on investment for years to come.
Category List
- 3D Point Cloud
- Artificial Intelligence
- Asset Management
- Digital Twin
- Featured
- Hardware
- Knowledge Graph
- LiDAR
- News
- Site Monitoring
- Vegetation Monitoring
- Virtual Reality
Recent Post
- Photogrammetry vs Image Processing: What’s the Difference and How Are They Used?
- Soil Adjusted Vegetation Index (SAVI): Definition and Application
- NDWI (Normalized Difference Water Index): Identifying Water Bodies with Remote Sensing
- Construction Management in the Digital Era: How GeoAI Transforms Projects with Data Analytics and AI
- What is Near Infrared (NIR)?